Boston EPDM roofing
Hello, and welcome to KTM Roofing & Exteriors. We are experts in EPDM roofing solutions in Boston. Our main goal is to provide quality EPDM solutions that protect for a long time and work well on both flat and sloped roofs.
Get a free estimate
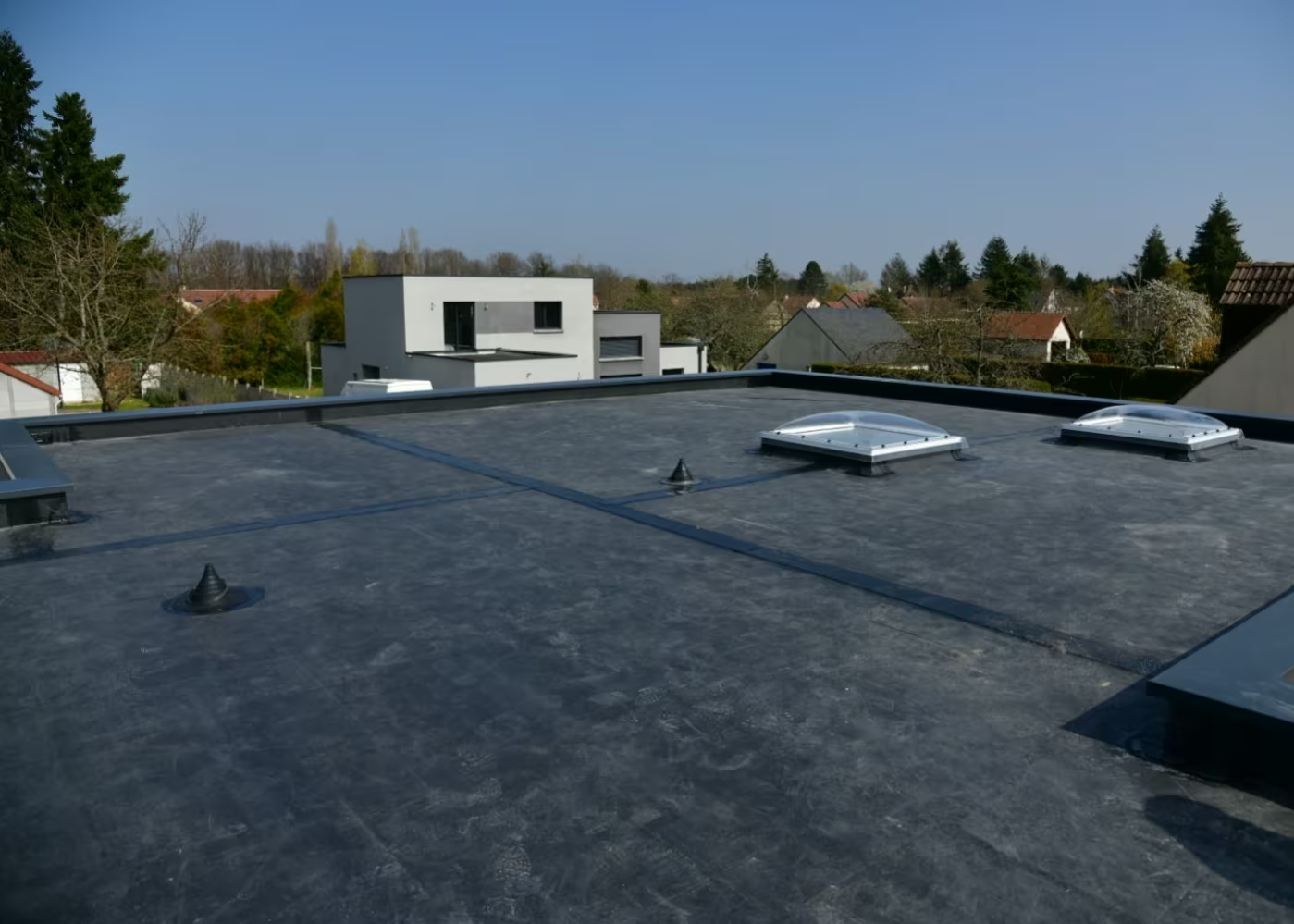
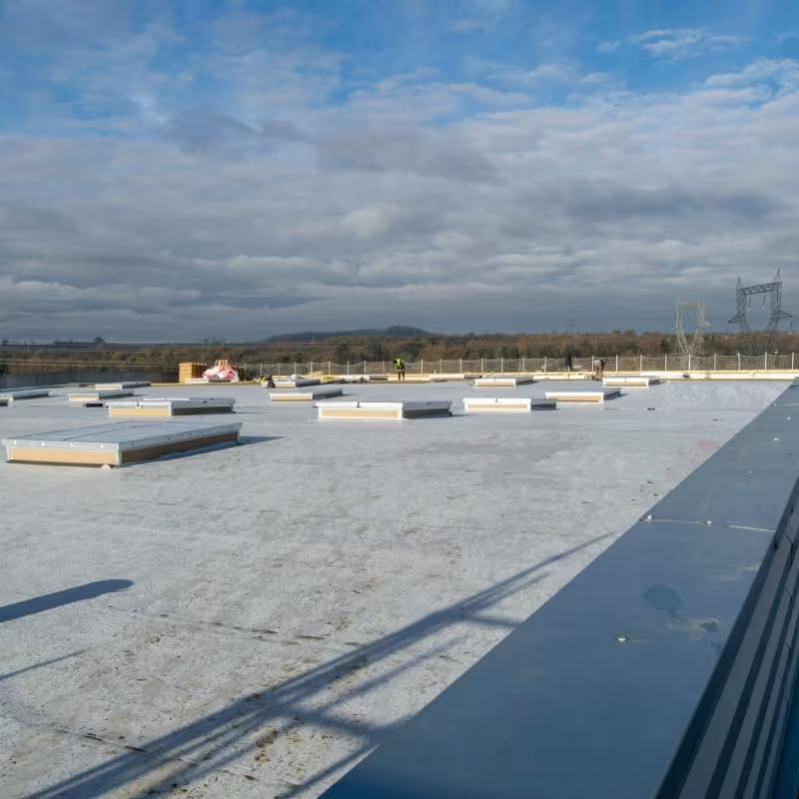
Why choose KTM's EPDM roofing for your property?
If you choose KTM's EPDM roofing, you're choosing roofing materials that are more resistant to damage and last longer. Our EPDM rubber roofs, which are made from ethylene propylene diene monomer, are great for the weather in Boston. They also make your home look better and use less energy. Our skilled Boston roofers will make sure that all of your roofing needs are met to the highest standards.
KTM's professional EPDM roofing installation process
Our installation process is meticulous, employing the best practices in the roofing industry. As a reputable commercial roofing contractor, we use high-quality EPDM rubber roofing materials to ensure that each installation meets your specific requirements and exceeds expectations.
Customization and style: EPDM roofing options with KTM
KTM has many roofing options, such as EPDM roofs that can be changed to fit different architectural styles. Our EPDM single-ply membranes come in a range of finishes to meet your needs, whether they're for a home roof or a business building.
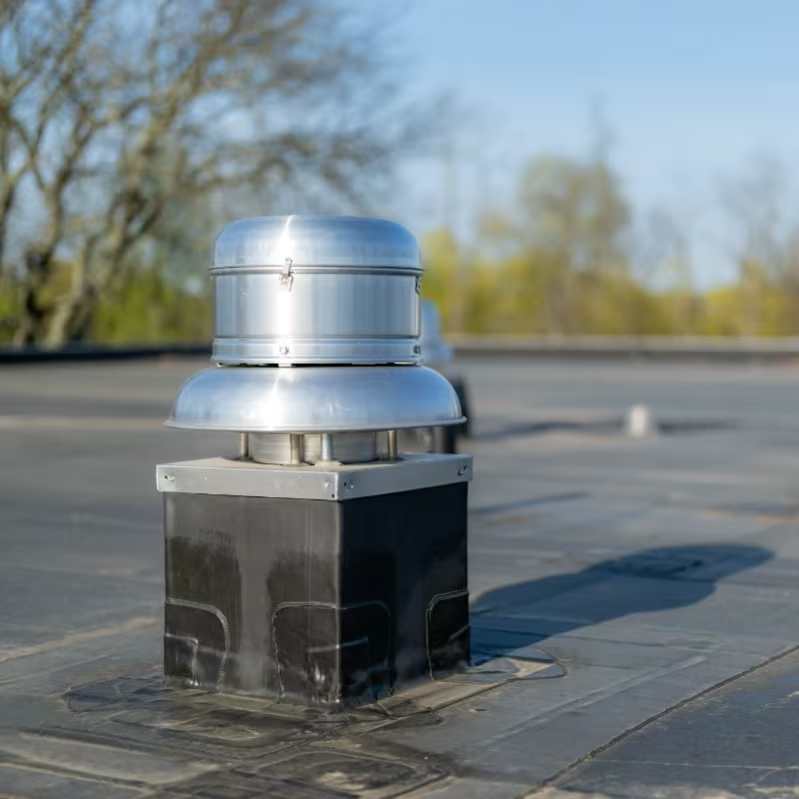
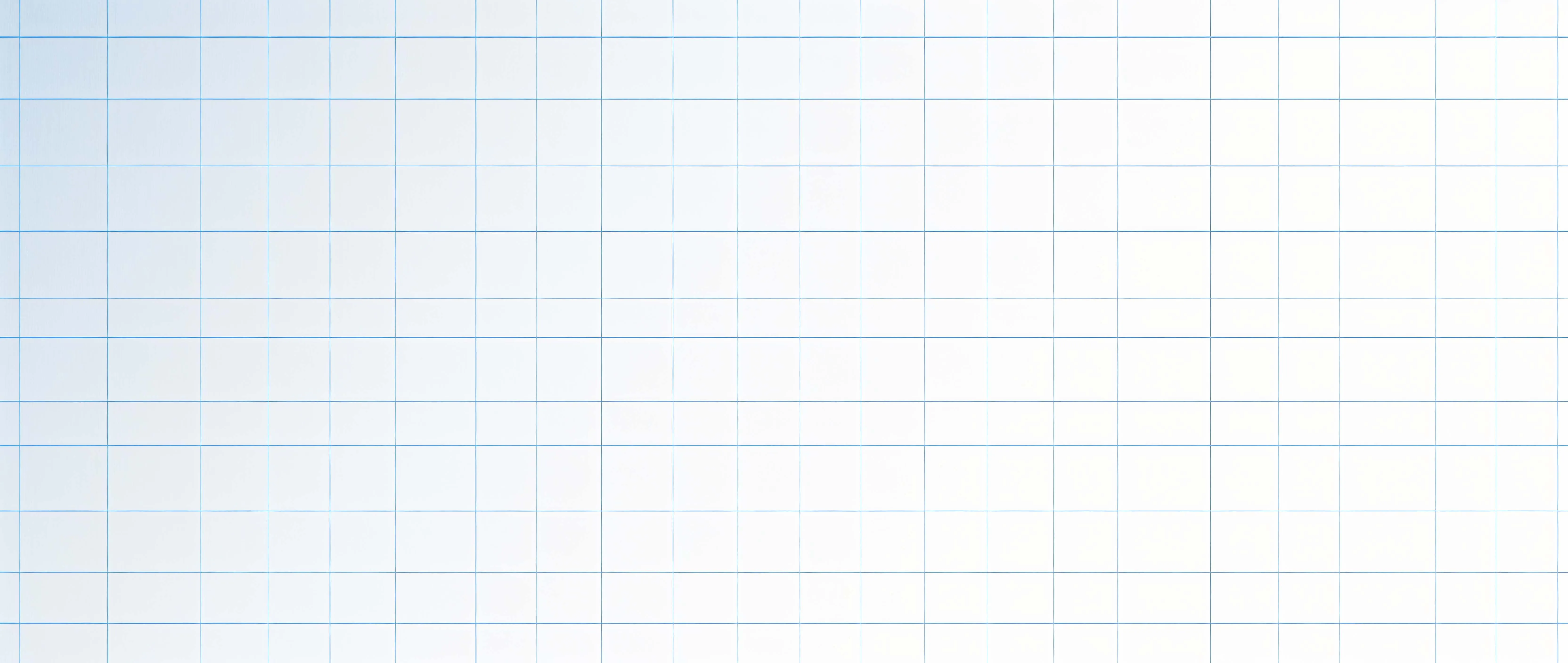
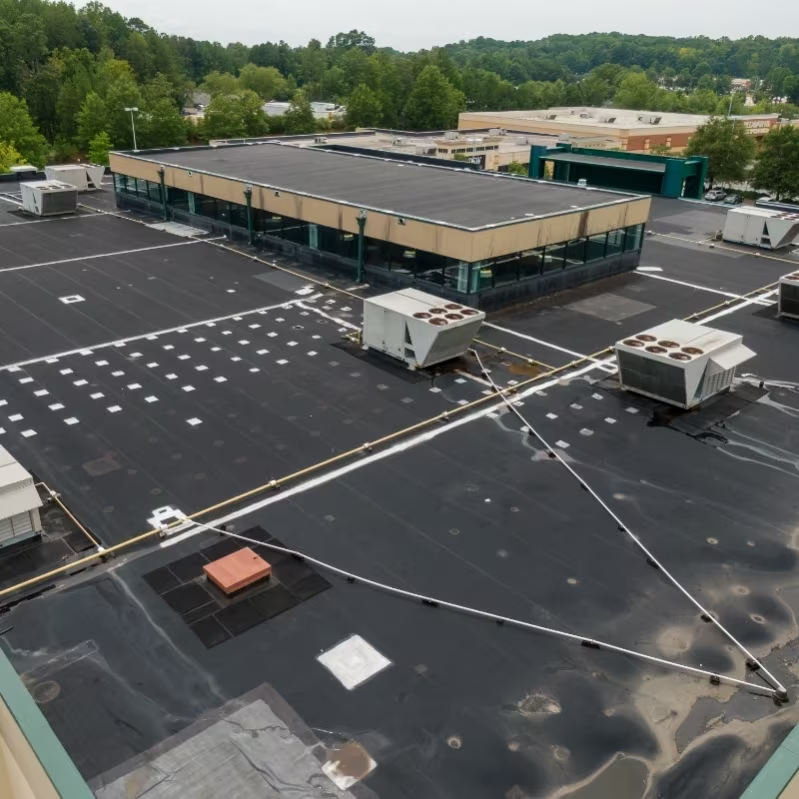
Weather resilience: EPDM roofing's strong suit
KTM’s EPDM roofing is renowned for its ability to withstand extreme temperatures and harsh weather conditions. This durability positions it as the perfect solution for Boston’s varied climate, providing enduring defense against roofing challenges.
Eco-friendly and energy efficient EPDM roofing
EPDM roofing from KTM is not only good for the environment, but it also saves a lot of energy and meets ENERGY STAR standards. This makes it a great choice for both new buildings and roof replacements since it can withstand thermal shock and save energy.
EPDM roofing for residential and commercial applications
Our EPDM roofing is versatile, catering to both residential and commercial roofing needs. As experienced roofing experts, we understand the unique requirements of different types of buildings and offer tailored EPDM rubber roof installation services.
Make KTM Roofing & Exteriors your choice for EPDM roofing
For top-tier EPDM roofing services in Boston, look no further than KTM Roofing & Exteriors. We are committed to providing cost-effective, high-quality roofing solutions. Our regular maintenance and repair techniques ensure your EPDM roof remains in excellent condition, solidifying us as your go-to roofing company.
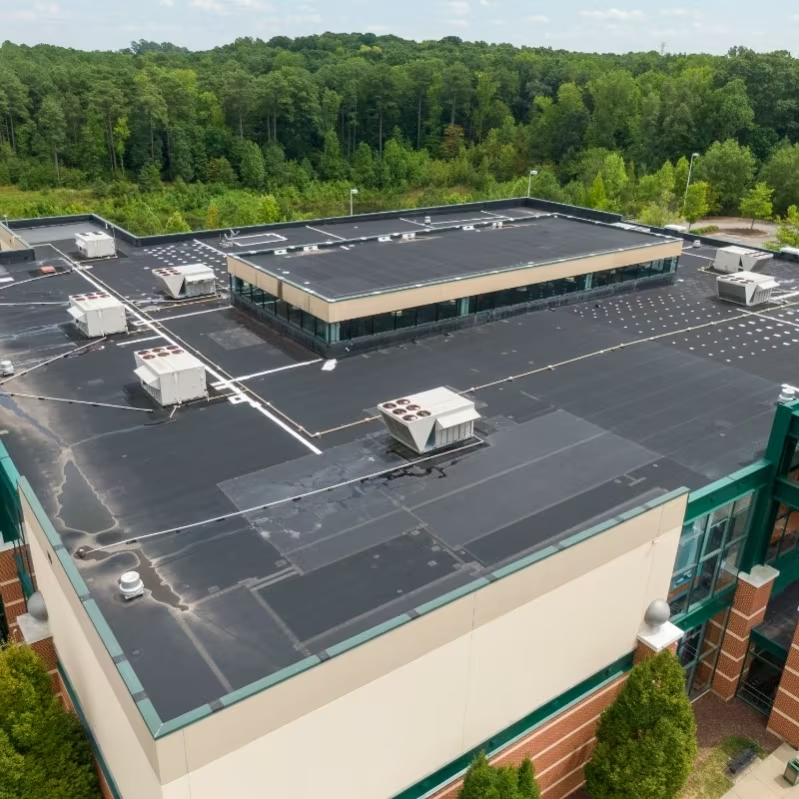
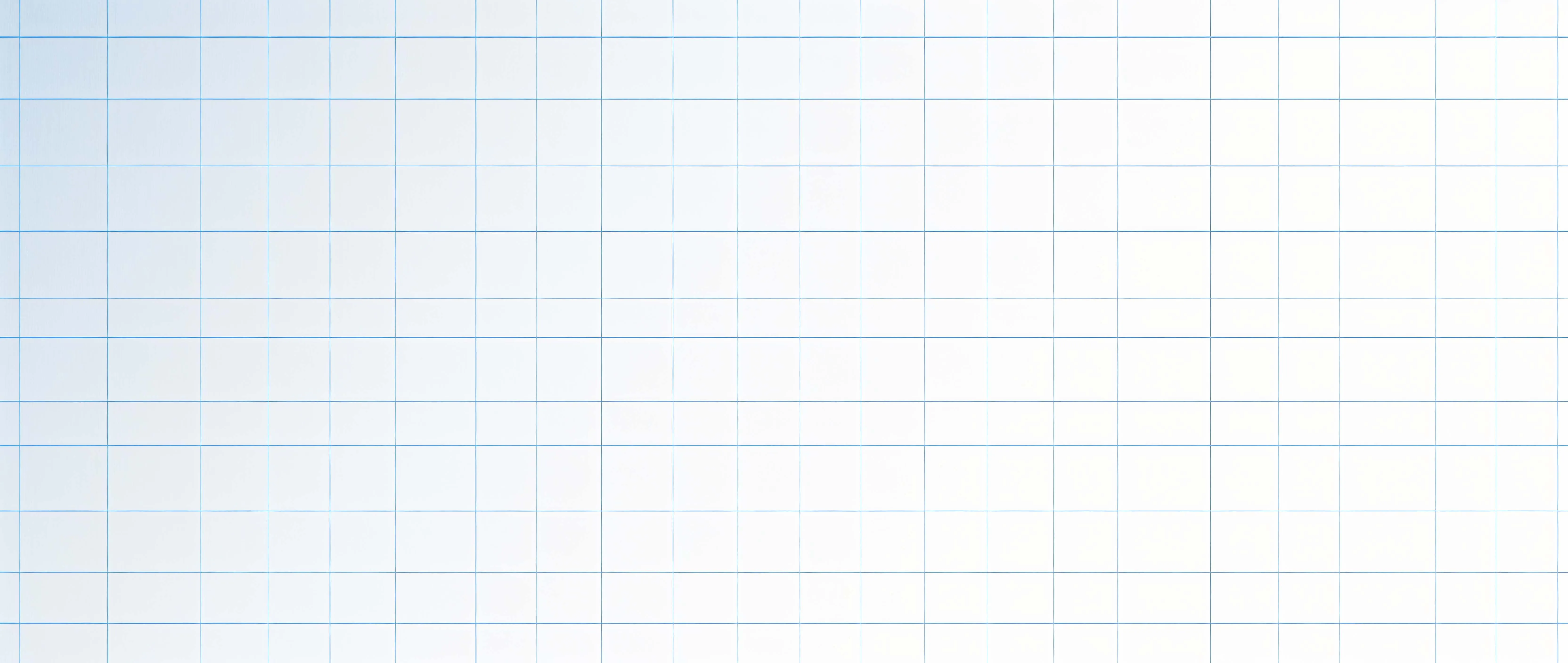
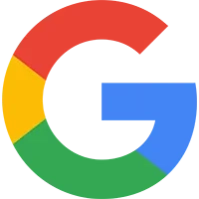
Hear from our happy customers
Linda Weatherbee
Charles Pouliot
Robert Fortunato
Raymond Madore
Contact us
Contact us today and take the first step towards enhancing your home or business in Boston, or surrounding areas!